Устройство вакуумных систем
Вакуумная система обычно состоит из откачиваемого объема, вакуумных насосов, вентилей и затворов. Соединение различных элементов вакуумной системы, в том числе и соединение откачиваемого объема с насосом, производится через соединительные трубопроводы.
Поскольку всякий трубопровод оказывает сопротивление потоку газа, то на концах трубопровода получается перепад давлений, вследствие чего эффективная быстрота откачки объема оказывается меньше, чем быстрота действия насоса.
Пропускная способность трубопровода (количество газа, проходящее через трубопровод в единицу времени) зависит прежде всего от степени вакуума, определяющей режим течения газа по трубопроводу. Кроме того, она зависит от размеров и формы сечения трубопровода, а также от температуры и рода откачиваемого газа.
На практике обычно приходится иметь дело с установками, в которых производится откачка воздуха при комнатной температуре, а трубопроводы, как правило, имеют круглое сечение При этом в низковакуумных коммуникациях чаще всего имеет место вязкостный режим течения газа, при котором пропускная способность трубопровода зависит как от его размеров, так и от давления газа. В высоковакуумных коммуникациях в условиях молекулярного режима течения, когда столкновения между молекулами газа практически отсутствуют, движение их по трубопроводу происходит за счет соударения со стенками, вследствие чего пропускная способность трубопровода зависит только от его размеров.
Для получения в вакуумной установке заданного предельного вакуума при минимальном времени, затрачиваемом на ее откачку, к конструкции вакуумной аппаратуры и материалам, используемым при ее изготовлении, предъявляется целый ряд требований.
Важнейшим из них является герметичность как самих деталей, из которых собрана вакуумная установка, так и мест их соединения
Для получения надежной герметичности при изготовлении вакуумных систем в первую очередь применяют материалы, имеющие плотную структуру, которая обеспечивает их газонепроницаемость даже при малых толщинах (стекло, малоуглеродистая и нержавеющая сталь, алюминий, медь и различного роДа сплавы).
Неразборные вакуумно-плотные соединения обычно осуществляются с помощью сварки и пайки, а для разборных соединений используются прокладки из резины, фторопласта, меди и алюминия.
Другое не менее важное требование заключается в том, что газоотделение стенок вакуумной аппаратуры должно быть минимальным. Поэтому используемый для изготовления вакуумной аппаратуры материал должен иметь при рабочей температуое минимальную упругость собственных паров и легко отдавать ранее поглощенные газы в процессе обезгаживания вакуумной установки. С этой точки зрения следует избегать применения пористых материалов, так как помимо значительной газопроницаемости они в течение длительного времени выделяют ранее поглощенные газы и пары Добиться достаточно чистой промывки материалов, имеющих пористую структуру, также не удается, поскольку грязь вместе с органическими растворителями забивается во все поры и трещины и удалить ее оттуда очень трудно. Для изготовления вакуумной аппаратуры преимущественно применяют материалы, имеющие плотную структуру, и прежде всего те из них, которые легко обрабатываются и полируются, что в значительной мере облегчает промывку деталей органическими растворителями для удаления жиров и других загрязнений с поверхности деталей перед их сборкой.
Следует также иметь в виду, что стенки вакуумной аппаратуры должны обладать прочностью, достаточной для того, чтобы противостоять внешнему атмосферному давлению.
В лабораторной практике при выполнении различного рода экспериментальных работ существенное значение имеет возможность быстрой переделки вакуумных установок, а поэтому в качестве конструкционного материала для их изготовления часто используется стекло. Стекло обладает способностью легко принимать и сохранять любую нужную форму, при прогреве с его поверхности достаточно легко удаляются ранее адсорбированные газы, оно практически газонепроницаемо, а давление насыщенного пара стекла настолько мало, что не оказывает влияния па степень вакуума в системе
Различные детали и участки вакуумной системы, изготовленные из стекла, могут иметь как подвижные, так и неподвижные соединения Неподвижные соединения осуществляются спаиванием стеклянных деталей при помощи газовой горелки, причем надежные спаи могут быть получены в том случае, если дета ди изготовлены из стекол с близкими коэффициентами теплового расширения, вследствие чего предотвращается возможность возникновения в месте спая внутренних напряжений, делающих спай хрупким и ненадежным Герметичность подвижных соединений (краны, шлифы) достигается за счет взаимной притирки соприкасающихся поверхностей с последующим нанесением на них специальной вакуумной смазки, обладающей нивкой упругостью пара (10-6—10~8 мм рт. ст. при 20°). Ловушки, краны и шлифы всех типов, а также другие стеклянные детали чаще всего изготовляются из стекол, обладающих высокой термической и химической стойкостью и хорошими изоляционными свойствами. Детали после изготовления, как правило, подвергаются отжигу при температуре около 500° для снятия внутренних напряжений.
Стеклянные краны, применяемые для разобщения участков вакуумной системы, бывают четырех типов: угловые (рис. 14, а), проходные (рис. 14, ‘б), трехходовые (рис. 14, в) и порционные (рис. 14, а). Основными частями каждого крана являются конусообразная пробка с отверстиями и муфта с патрубками, служащими для присоединения крана к вакуумной системе.
В том случае, если прибор после откачки необходимо наполнить каким-либо газом до определенного малого давления, обычно применяют порционный кран, у которого внутри пробки впаяна трубочка небольшого объема. При повороте крана в сторону баллона с газом эта трубочка, будучи запаянной с одного конца, наполняется газом до определенного давления. При повороте пробки крана на 90° трубочка отделяет определенную порцию газа. При дальнейшем повороте пробки крана трубочкой в сторону вакуумной системы газ из трубочки распространяется по всему объему вакуумной системы, чем и осуществляется точная дозировка степени наполнения.
В практике конструирования и эксплуатации вакуумных систем часто приходится устанавливать стеклянные детали на металлических установках и, наоборот, металлические детали на стеклянных установках. (Кроме того, иногда возникает необходимость вводить из атмосферы в вакуумную систему электрические проводники. В связи с этим появляется необходимость в осуществлении вакуумно-плотных спаев металлов со стеклом.
Основные требования к материалам, применяемым для изготовления спаев, сводятся к следующему:
-
1. Металлы и сплавы должны обладать близкими линейными коэффициентами теплового расширения по отношению к стеклам, в которые они впаиваются (за исключением «несогласованных» спаев меди со стеклом).
-
2. Металлы и сплавы должны хорошо смачиваться размягченным стеклом, так как спаи должны быть газонепроницаемыми,
т. е. вакуумно-плотными.
3. Металлы и сплавы должны быть достаточно тугоплав
кими, чтобы выдерживать нагрев, необходимый для впаивания их в стекло.
Основная трудность в выполнении таких спаев заключается в различии линейных коэффициентов теплового расширения металлов и стекол. Поэтому следует различать «согласованные» и «несогласованные» спаи металла со стеклом. IK первым относятся спам, в которых ме
талл спаивается непосредственно со стеклом, причем подбираются стекло и металл с близкими друг к другу линейными коэффициентами
теплового расширения. Ко
вторым относятся спаи, в которых линейный коэффициент теплового расширения металла значительно отличается от линейного коэффициента теплового расширения стекла, а опасные
напряжения, которые могут возникнуть при этих условиях, ослабляются путем применения мягких металлов. Иногда для этой цели используют промежуточные стекла и переходные спаи, причем спай между металлом и последним из стекол
является спаем «согласованного» типа.
Типичным примером «согласованного» спая металла со стеклом являются широко распространенные штампованные стержневые спаи, когда проволоки проводятся через стеклянную трубку с фланцем (тарелочкой), которая затем нагревается до размягчения в определенном месте и сжимается клещами так, что проволоки оказываются запресованными в стекле.
Типичным примером «несогласованного» спая является трубчатый спай меди со стеклом (рис. 15). В этом случае концы медной трубки растачивают на конус с очень малой толщиной стенки (несколько сотых долей миллиметра), к которой затем припаивается стекло. В этих спаях медь имеет более высокий коэффициент теплового расширения, чем стекло. Однако, имея малую толщину стенок, она обладает мягкостью и текучестью,

достаточными для того, чтобы деформироваться при изменении температуры и обеспечить таким образом ослабление напряжений в месте спая.
Для впайки тонких проволок (диаметр которых не превышает 1 мм) в легкоплавкое стекло, линейный коэффициент теплового расширения которого обычно лежит в пределах (80 — 100)-10-7, чаще всего используют платинит. Платинитовая проволока состоит из железо-никелевого сердечника и тонкой медной оболочки, покрытой закисью меди и бурой. Закись меди способна растворяться как в самой меди, так и в стекле, что обеспечивает хорошую смачиваемость стеклом поверхности платинита.
В тех случаях, когда необходимо подводить значительные токи (десятки ампер), в качестве материалов для впаев в стекло применяют молибден и вольфрам в виде проволок и стержней диаметром от 0,5 до 8 мм, причем перед впайкой место впая предварительно оплавляется стеклом. Для впаивания проволочных вводов ив молибдена и вольфрама используются тугоплавкие сорта стекол, линейный коэффициент теплового расширения которых лежит в пределах (40 — 50) -К)-7.
Для изготовления спаев металлических и стеклянных трубок используются также специальные сплавы. Так, для спаев с легкоплавким стеклом используются высокохромистые стали (феррохром, фуродит), для спаев с тугоплавкими стеклами применяют ковар (сплав никеля, кобальта и железа). Ковар позволяет осуществить разнообразнейшие конструкции дисковых, кольцевых и цилиндрических спаев со стеклом, ряд примеров которых представлен на рис. 16.
В отличие от лабораторных вакуумных установок небольшого объема, состоящих почти целиком из стекла, корпуса больших металлических выпрямителей, электронных микроскопов, печей для вакуумной пайки и плавки, установок для нанесения покрытий под вакуумом и другой вакуумной аппаратуры чаще всего изготовляются путем сварки стальных листов различной толщины и геометрических размеров. Металлические огливки из-за своей пористой структуры для изготовления высоковакуумной аппаратуры, как правило, не применяются. Исключение составляет качественное чугунное и стальное литье, которое используется для изготовления корпусов вращательных насосов предварительного разрежения. Однако в этом случае к отливкам предъявляются очень жесткие требования как в части отсутствия трещин, пор и раковин, так и с точки зрения газонепроницаемости используемого материала. Из стального прокат^ для изготовления сварных корпусов наиболее широкое применение имеют малоуглеродистая и нержавеющая стали. Из цветных металлов чаще всего используют алюминий, медь, латунь.
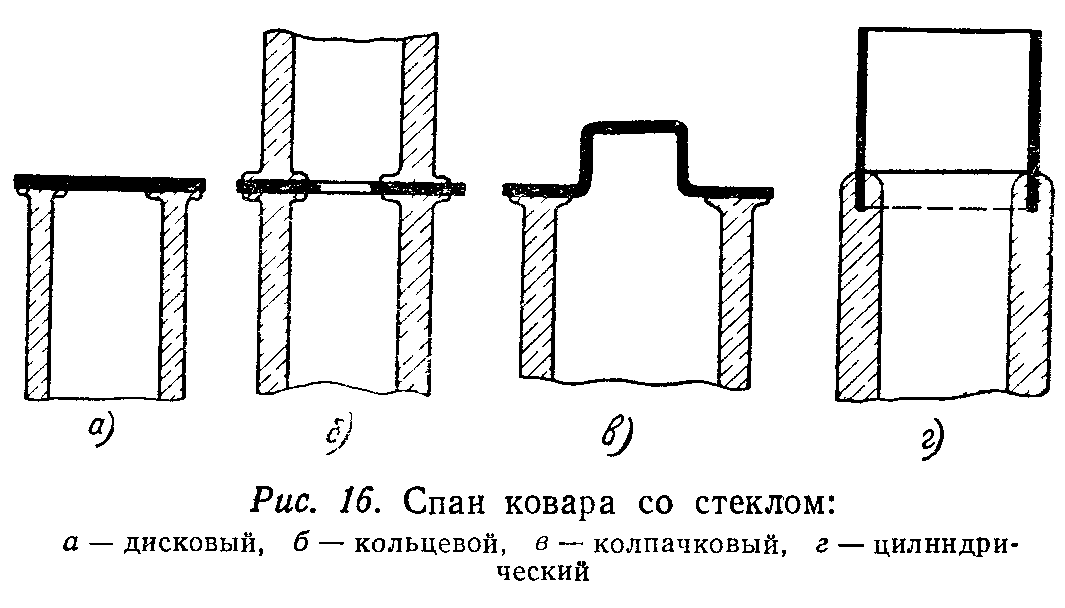
Неразборные вакуумные соединения осуществляются за счет сварки и пайки металлических деталей. Поэтому одним из важнейших свойств материалов, применяемых для изготовления вакуумных систем, помимо их большой плотности и малого газовыделения, является их способность к свариванию и спаиванию. Разборные вакуумно-плотные соединения осуществляются с помощью резиновых и металлических прокладок. Для умеренных температур и нагрузок наиболее часто в качестве прокладочного материала используется вакуумная резина. На рис. 17 показаны два широко распространенные типа фланцевых соединений для труб диаметром от 10 до 500 мм, уплотненных кольцевой прокладкой, вырезанной из вакуумной резины.
Для уплотнения металлических и стеклянных труб небольшого диаметра (меньше 30 мм) применяют изображенное на рис. 18 грибковое уплотнение, которое осуществляется за счет плотного прилегания к трубе кольцевой резиновой прокладки, сжимаемой гайкой и шайбой.
Значительное выделение газов из резины и недопустимость прогрева установки с целью ее обезгаживания при использовании резиновых уплотняющих прокладок существенно ограничивают применение резины в тех случаях, когда в вакуумной установке требуется получить давление ниже 10-6 мм рт. ст.
В таких случаях широкое применение находит изображенное на рис. 19 разборное вакуумно-плотное фланцевое соединение с металлической прокладкой, имеющее канавочно-клиновой уплотняющий профиль. В качестве прокладок используются кольца из

листовой холоднокатаной меди или листового мягкого алюминия толщиною 0,2—1 мм. Такого рода фланцевые соединения допускают длительный нагрев до температуры 600° при использовании медных прокладок и до 400° при использовании прокладок из алюминия.
Помимо резиновых и металлических прокладок в качестве уплотнительного материала иногда применяется фторопласт (тефлон). Он выделяет значительно меньше газов, чем резина, химически стоек в широком диапазоне температур, допускает нагрев до 250°. Хорошие электроизоляционные свойства фторопласта позволяют применять его для электрических вводов в вакуумную систему.
Для осуществления перемещения и вращения отдельных элементов аппаратуры в вакууме без нарушения герметичности соединения в зависимости от технических требований (диаметра вала, числа оборотов, величины передаваемого усилия, длины продольного перемещения и т. д.) используют самые различные устройства.
Если через стенку вакуумной камеры необходимо передавать вращение с небольшим числом оборотов в минуту, то для этого в простейшем случае можно использовать обыкновенные шлифы со смазкой, изготовленные из стекла, латуни или меди.
Для осуществления возвратно-поступательного перемещения штока в стенке вакуумной камеры часто используются гофрированные трубки (сильфоны), изготовленные из стали, томпака, меди или латуни. За счет упругой деформации гофр сильфоны можно легко сгибать, растягивать и сжимать. Сильфонное уплотнение перемещающегося стержня показано на рис. 20. Сильфон 1 припаян сверху к крышке 2, а снизу к фланцу 3. В этом фланце имеется направляющая втулка 4, в которой центрируется и перемещается стержень 5, укрепленный на резьбе в крышке 2. Для откачки воздуха из внутренней полости сильфона в стержне 5 имеются пазы 6. Уплотнение фланца 3 в соединении с фланцем
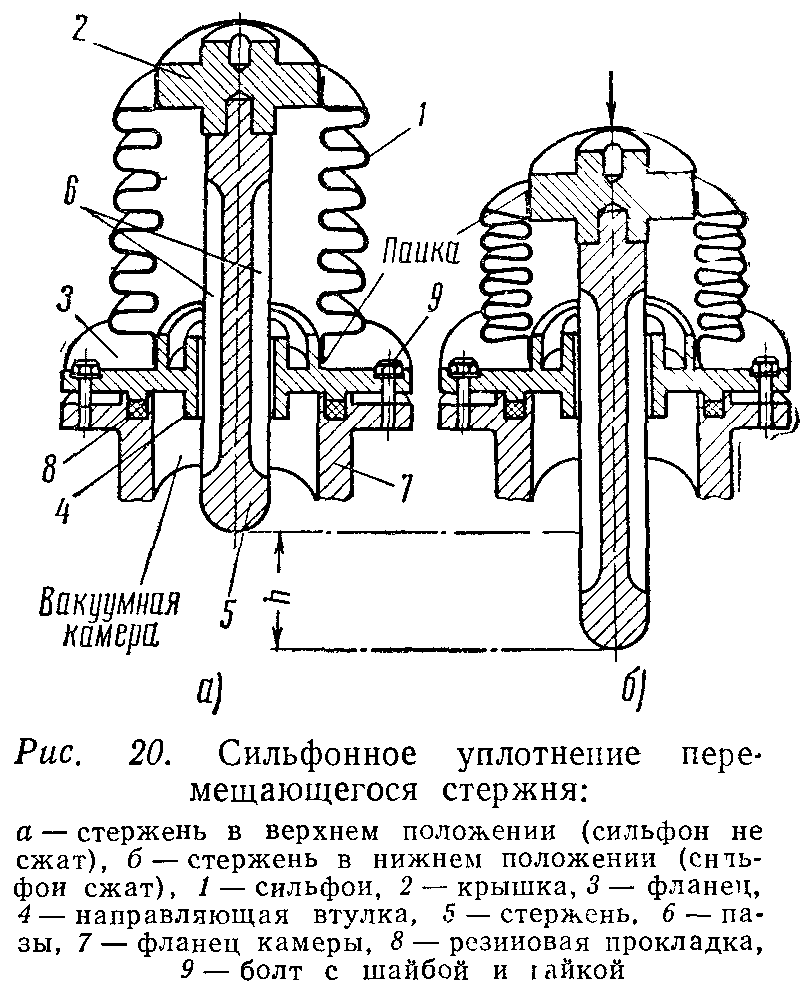
камеры 7 осуществляется при помощи резиновой кольцевой прокладки 8, прижимаемой при завинчивании болтов 9. Крышка 2 на разборном соединении жестко связана с управляющей системой, которая выполняется с учетом того, что сильфон под действием атмосферного давления стремится сжаться (например, при диаметре сильфона 50 мм, сжимающее усилие составляет около 20 кг).
Сильфонное соединение используют также для передачи колебательного й вращательного движений в вакуумную установку.
Для передачи движения в вакуум используют также различные уплотнения сальникового типа. На рис. 21 показан общий вид такого рода уплотнения с применением резиновых прокладок и металлических шайб. Для уплотнения служат две прокладки ив маслостойкой вакуумной резины 4, между которыми проложена металлическая шайба 5. На верхнюю резиновую прокладку накладывается еще одна металлическая шайба 6, прижимаемая сверху зажимной гайкой 3. Для надежной работы уплотнения вал 1 должен быть хорошо, но не слишком обильно, смазан

высококачественной вакуумной смазкой.
Для разобщения отдельных частей вакуумной системы в промышленных вакуумных установках широкое применение находят вентили и затворы. Как правило, вентиль или затвор не пропускает воздух из атмосферы при любом положении клапана, а при разумно выбранной конструкции срабатывает достаточно легко и быстро, не требуя большого усилия для надежного уплотнения клапана.
Для трубопроводов предварительной откачки, а также для тех высоковакуумных коммуникаций, где не требуется большая пропускная способность, чаще всего применяются двусторонние вентили. У таких вентилей диаметр максимального проходного отверстия обычно не превышает 160 мм. Конструкция этих вен-титей во многохм напоминает вентили, применяемые в водопроводных и газовых системах, но обладает своими характерными особенностями, связанными с повышенными требованиями к герметичности.
Наиболее широко распространенная конструкция вакуумного
вентиля с резиновым уплотнением седло-клапан изображена на рис. 22. В резьбовой канавке крышки 7 вентиля перемещается шток 6 с закрепленным снизу клапаном 3. Крышка вентиля герметично соединена с его верхним патрубком благодаря применению разборного вакуумно-плотного соединения с использованием уплотняющей кольцевой прокладки 9, вырезанной из листовой вакуумной резины. Сильфон 5 одним своим краем припаян к
клапану, а другим к крышке, благодаря чему осуществляется уплотнение резьбовой канавки между штоком и крышкой корпуса. Сильфонное уплотнение вращающегося штока обеспечивает хорошую герметичность поворотного механизма, но срок службы сильфона невелик, а замена его связана с трудностями. Поэтому для более надежной и безаварийной работы вентиля зачастую предпочитают пользоваться не сильфонным уплотнением перемещающегося штока, а уплотнением с использованием резиновых прокладок.
Для трубопроводов, имеющих небольшое проходное отверстие, в установках с особо жесткими требованиями к предельному вакууму применяются вентили с металли-
ческим уплотнением седло-клапан. Изображенный на рис. 23 цельнометаллический вентиль используется в установках, имеющих давление порядка 1СГ7 мм рт. ст. при небольших скоростях откачки. Уплотнение в такого рода вентилях осуществляется по линии плотного прилегания конического клапана 1 к цилиндрическому седлу 2. В целях получения надежного уплотнения сменный клапан делают из мягкого материала (‘медь, никель, алюминий, реже латунь), а седло — из твердого материала (закаленная сталь). Вакуумная плотность цельнометаллических вентилей обеспечивается при помощи мембран и сильфонов. Герметичное соединение мембраны с корпусом вентиля и с подвижным клапаном осуществляется при помощи разборного соединения с канавочно-клиновым уплотняющим профилем, что позволяет, в случае необ* ходимости, легко заменить мембрану и клапан. Применение штока с дифференциальной резьбой позволяет осуществлять точное перемещение клапана.
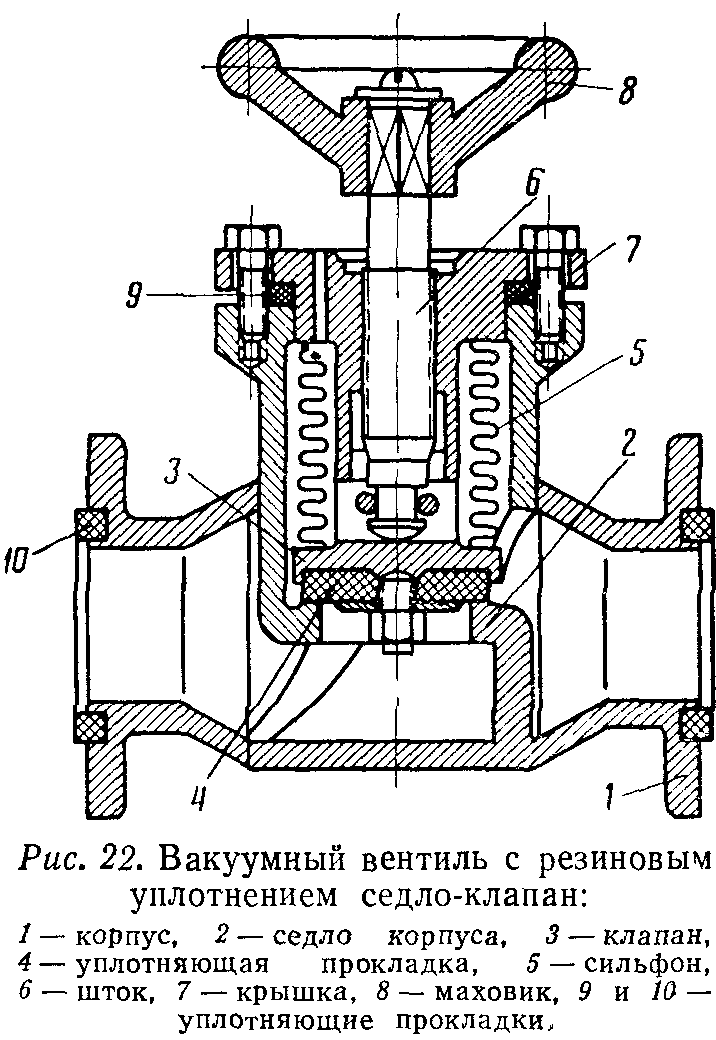
В том случае, когда наряду с большой пропускной способ- > ностью требуется значительная быстрота манипуляции вентилем, обычно используются вакуумные затворы.
Промышленностью выпускаются затворы с диаметрами условного прохода от 85 до 500 мм. Конструкция вакуумных ватворов
предусматривает их установку в специальных переходных патрубках между насосом и откачиваемой системой.
Механизм металлического вакуумного затвора с резиновым уплотнением, изображенный на рис. 24, расположен на отдельном фланце 1. Необходимое перемещение перекрывающего диска 2 при закрывании и последующем поджатии его к уплотняющей прокладке 3 осуществляется посредством рычажно-эксцентрикового механизма 4. Соединение привода с эксцентриковым валом механизма осуществляется посредством муфты 5. Уплотнение вала осуществляется за счет использования резиновых уплотнителей и металлических шайб.
Высоковакуумные насосы присоединяются обычно к вакуумным системам не непосредственно, а через переходные коммуникации; кроме того, между насосом и системой в большинстве случаев устанавливают вакуумные затворы, позволяющие отключать насос от системы, а также охлаждаемые ловушки для улавливания паров рабочей жидкости, уходящих из насоса в систему.
В связи с этим промышленностью выпускаются специальные вакуумные откачные установки, включающие в себя высоковаку-
умный пароструйный насос, ловушку, охлаждаемую жидким азотом, и переходный патрубок с затвором. Эти установки называются вакуумными агрегатами.
Изображенный на рис. 25 типичный вакуумный агрегат представляет собой вакуумную установку, состоящую из паромасля-ного насоса 1, укрепленного на раме 2, вертикального патрубка 3 для присоединения к откачиваемому объему, высоковакуумного затвора 4, щитка электроуправления 5, вакуумной ловушки 6 и сосуда Дьюара 7.
Патрубок 3 представляет собой сварную конструкцию с тремя присоединительными фланцами, из которых один служит для присоединения агрегата к откачиваемому объему, второй — для присоединения патрубка к фланцу затвора и третий — для присоединения к крышке.,
Система охлаждения агрегата обеспечивает подачу проточной воды в маслоотражатель и паромасляный насос. Установленный

на агрегате гидро-контакт обеспечивает нормальное охлаждение агрегата и срабатывает, выключая электронагреватель насоса, при уменьшении расхода охлаждающей воды ниже нормы
Быстрота действия современных вакуумных агрегатов достигает нескольких тысяч литров в секунду.